Assembling Nanoparticles on Liquid Interfaces Leads to Fascinating New Materials
30 Aug, 2007 02:46 pm
Stefan A. F. Bon discusses how you can use liquid-liquid interfaces as a tool to assemble nanoparticles into larger structures. His group is looking at the fabrication of these complex supracolloidal structures using a combination of interface-driven assembly of particles and macromolecular (plastic/polymer) chemistry.
Scientists have therefore been looking at ways to drive the assembly process of small particles, which often are dispersed in a liquid. We like to call this area supracolloidal chemistry as the organisation of colloidal nanoparticles into larger structures shows resemblance to the self-assembly of molecules in the area of supramolecular chemistry.1
Innovative tools to drive the assembly process include the use of electric fields,2 convective flows,3 and the use of patterned surfaces and templates4 to guide to assembly and ordering of nanoparticles and colloids. An interesting approach is to use a soft interface, i.e. liquid-liquid or liquid-gas, as a tool to capture particles and guide their assembly, whereby the interface acts as template. That solid particles can adhere strongly to liquid-liquid interfaces was first described by Ramsden and Pickering in the early 1900s. The phenomenon is more commonly known as Pickering stabilization, and is used widely in a variety of disciplines, e.g. food, cosmetics and crude-oil recovery, to stabilize emulsions.
In our group we look at this interface-driven assembly process of colloidal particles and combine this with polymer chemistry to create a variety of complex supracolloidal structures.1
Fig 1. Pickering miniemulsion Polymerization: Nanoparticles are assembled small droplets of monomer (diameter 150-800 nm). These droplets are subsequently polymerized via conventional free radical polymerization to yield hybrid armored polymer latexes.
We demonstrated the principle of a Pickering (mini)emulsion polymerization.5,6 By using nanosized clay discs of 25 nm in diameter and 1 nm height we showed the fabrication of clay armored polymer latexes, with accurate control of particle diameters in the range of 150-800 nm. These inorganic-polymer hybrid latexes show remarkable properties upon film formation, such as flame retardancy and scratch resistance. We now can fabricate hybrid armored latexes with an overall solids content easily exceeding 40wt%, clearly showing that industrial scale-up is feasible.
We also fabricate raspberry-shaped microcapsules. The assembly process is combined with a scaffolding polymerization step. The latter controls the robustness of the capsules, whether they are rigid, or flexible. We used polymer microgel particles7 and titanium dioxide nanoparticles8 as supracolloidal building blocks. Beside the obvious application-driven functionality of the building blocks, a raspberry-shaped morphology can have great impact in microcapsule diffusion, adhesion and their release behaviour of active ingredients.
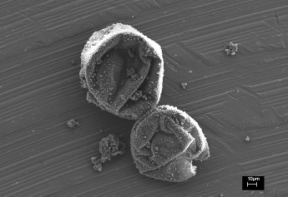
We showed for the first time the manufacturing of cellular polymer monoliths, or highly porous foams with the aid of nanoparticles.9 These materials are also known as poly(HIPE)s. Their high specific surface area makes them ideal candidates for stationary phases in separation and analytical science, especially when we now can functionalize each cell surface with nanoparticles! We showed this using two different types of particles, making three different cellular designs opening the door to creations of specific cell micro-environments to perform multi-step reactions in one fluidic device.
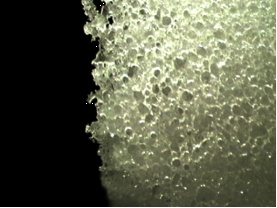
Fig 3. Cellular Polymer monolith made via Pickering high internal phase emulsions.9
We currently are looking at fabrication of complex nano-patterned silica microstructures, inspired by the skeletons made from silica and calcium carbonates in organisms such as diatoms and coccolithophorids, types of phytoplankton. Furthermore, we are investigating the fabrication of non-spherical liquid droplets; are looking at alternative forces, in addition to surface tension, to control the assembly process; and are expanding in areas of microfluidics and the manufacturing of hybrid scaffolds for tissue regeneration using photolithographic approaches. In conclusion, enough excitement in this intriguing and rapidly developing field of supracolloidal chemistry!
References:
1.) Colver, P. J.; Chen, T.; Bon, S. A. F. Macromol. Symp. 2006, 245-246, 34-41. 2.) Velev, O. D.; Bhatt, K. H., Soft Matter 2006, 2, 738-750. 3) Jiang, P.; Bertone, J. F.; Hwang, K. S.; Colvin, V. L., Chem. Mater. 1999, 11, 2132-2140. 4) van Blaaderen, A.; Ruel, R.; Wiltzius, P., Nature 1997, 385, (6614), 321-324. 5) Cauvin, S.; Colver, P.J.; Bon, S.A.F. Macromolecules, 2005, 38, 7887-7889. 6) Bon, S.A.F.; Colver, P.J. Langmuir, 2007, 23, 8316-8322. 7) Bon, S.A.F.; Cauvin, S.; Colver P.J. Soft Matter 2007, 3, 194-199. 8) Chen, T.; Colver P. J.; Bon S.A.F. Adv. Mater. 2007, ASAP. 9) Colver P. J.; Bon, S.A.F. Chem. Mater. 2007, 19, 1537-1539.
Nice work, but it would useful to similar approaches such as Fossilized Liquid Assembly which is listed in http://www.nist.gov/public_affairs/techbeat/tb2006_1012.htm#liquid
and published in
* J.J. Benkoski, H. Hu, and A. Karim. Generation of hierarchical topologies from photocrosslinkable, particle-stabilized emulsions. Macromolecular Rapid Communications. Aug. 2, 2006